The introduction of slotted bearing technology in universal joints has significantly impacted the heavy-duty truck industry by enhancing the durability, reliability, and efficiency of drivetrains in trucks that are subjected to demanding working conditions. Universal Joint with Slotted Bearings, which are key components in connecting shafts to transmit power in heavy-duty vehicles, have evolved over the years to meet the increasing mechanical demands of the trucking industry. The integration of slotted bearings into these joints has proven to be one of the pivotal innovations that have pushed the boundaries of vehicle performance and longevity.
At the heart of this innovation lies the slotted groove on the bottom of the bearing cup, which allows for a plate to fit into the groove and hold the cups securely with bolts. This design provides an additional layer of strength and stability that is particularly crucial for heavy-duty trucks, which operate under high torque and carry large loads. The slotted bearing structure is better equipped to withstand the immense forces generated by the driveline, thereby reducing wear and tear. Compared to traditional universal joints, which are prone to loosening or premature failure under high stress, the slotted bearings’ bolted connection ensures a more secure fit, limiting the chance of mechanical failure. This improvement in joint stability allows for smoother power transmission between the engine and the wheels, thereby enhancing vehicle performance, especially in heavy-duty applications such as construction, long-haul transport, and mining.
In terms of commercial value, the adoption of universal joints with slotted bearings has had a profound economic impact on the heavy-duty truck industry. These joints reduce the frequency of component failures, leading to longer service intervals and lower maintenance costs for fleet operators. For industries relying on heavy-duty trucks, such as logistics, construction, and agriculture, the reduction in downtime and repairs directly translates into increased productivity and cost savings. Although universal joints with slotted bearings are typically more expensive upfront than conventional alternatives, their extended service life and superior performance make them a cost-effective choice over time. The market for these components has expanded as truck manufacturers and operators prioritize durability and reliability, with major players in the industry continually refining their designs to cater to the growing demand for high-performance driveline components.
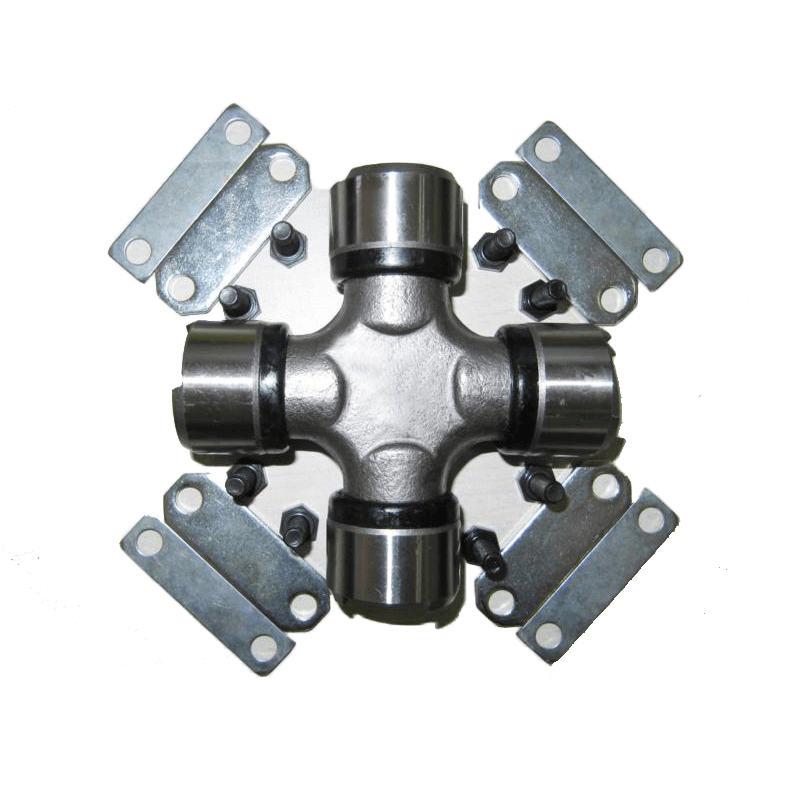
From a technical perspective, the introduction of slotted bearings addressed several limitations of earlier designs. Traditional universal joints often struggled with misalignment and uneven wear, leading to premature failure. Slotted bearings, with their precise groove and bolted attachment, reduce the likelihood of such issues, ensuring a more consistent load distribution and improving the overall lifespan of the component. Furthermore, the slotted bearing design enhances the joint's ability to handle larger misalignments without sacrificing performance, a critical advantage for heavy-duty trucks that often operate under harsh conditions, including uneven terrains and heavy loads. This technical advancement not only improved the operational efficiency of these vehicles but also raised the bar for engineering standards in the industry.
In addition to the practical benefits, slotted bearing technology reflects broader trends in engineering and technological innovation. As industries become increasingly dependent on heavy-duty trucks for transportation and infrastructure development, there has been a corresponding push toward developing components that are more robust, efficient, and capable of withstanding extreme conditions. The slotted bearing universal joint is an example of how small yet significant innovations in design can lead to transformative changes in vehicle performance. This development also highlights the importance of collaboration between engineers, manufacturers, and end-users in pushing the limits of what heavy-duty trucks can achieve, both in terms of power transmission and mechanical resilience.
Historically, the evolution of universal joints with slotted bearings can be seen as part of a larger narrative in the advancement of automotive engineering. The need for more reliable and durable driveline components became increasingly apparent as trucks grew larger and more powerful, with higher payload capacities and tougher operating environments. Innovations like the slotted bearing not only improved the mechanical efficiency of trucks but also set a new standard for future developments. The heavy-duty truck industry has long been a driving force behind the demand for stronger, more efficient components, and the introduction of slotted bearings played a pivotal role in meeting these evolving needs.
Contact Us