Among the common configurations, the universal joint with inside snap ring and its outside snap ring counterpart stand out for their distinct structural differences, which in turn influence performance, installation, and maintenance. While both are used to connect shafts and transmit torque across misaligned angles, their suitability often depends on the precision demands, space constraints, and operational loads of the system in question.
The universal joint with inside snap ring is engineered with the snap ring positioned within a groove located on the inner side of the yoke, securing the bearing cups from the inside. This internal retention system provides a cleaner exterior profile, which is especially beneficial in compact installations where clearance is limited. It also allows for more consistent axial positioning of the cross kit within the yoke, contributing to better alignment and balanced rotation. On the other hand, outside snap ring types use external grooves on the cup to hold the snap ring, making the joint slightly bulkier but potentially easier to inspect during routine maintenance.
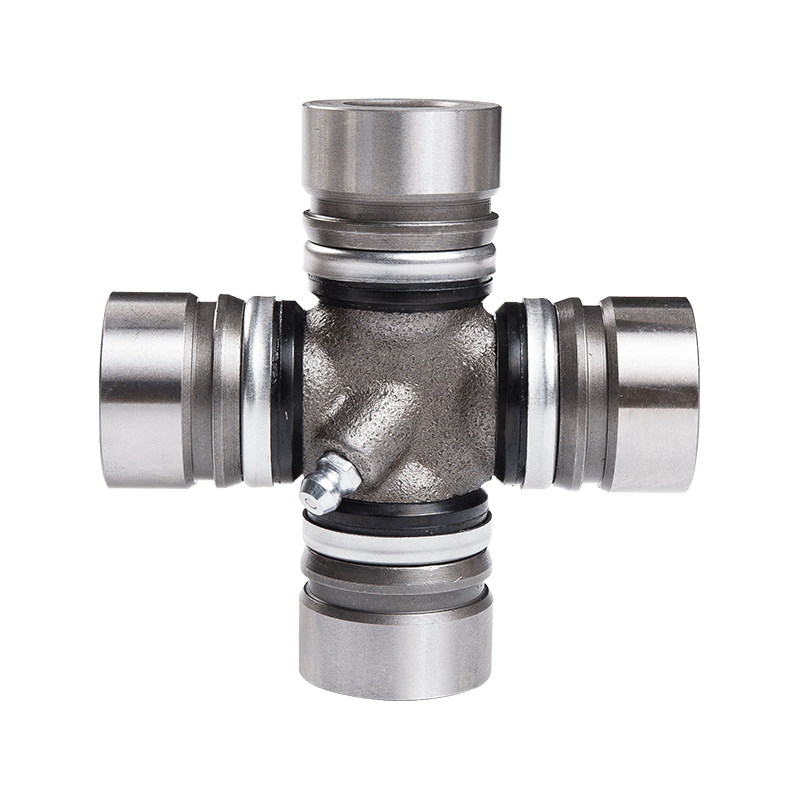
From a performance standpoint, the choice between inside and outside snap ring types can also affect the durability of the universal joint over time. Inside snap ring designs are typically less prone to debris interference and corrosion at the locking points, a factor that becomes particularly valuable in agricultural or off-road applications where exposure to harsh environments is routine. In contrast, outside snap ring types offer the advantage of quicker field disassembly, which can be a logistical benefit in high-maintenance industrial settings. For customers balancing ease of service with performance stability, understanding these practical trade-offs is key.
Installation practices vary slightly as well. Universal joint with inside snap ring often require greater precision during assembly to ensure that the snap rings seat properly within the yoke grooves, but once in place, they provide a solid and reliable hold. Outside snap ring assemblies tend to be more forgiving during installation but can loosen over time if not carefully maintained. Manufacturers like us, with years of experience in global export and OEM supply, often recommend the inside snap ring design for demanding applications where performance reliability is prioritized over speed of replacement.
As a supplier committed to long-term partnerships, we’ve seen many cases where a customer’s performance issues stemmed from mismatched joint types rather than flawed components. Choosing between a universal joint with inside snap ring and one with an external locking system isn’t just a matter of preference—it’s a technical decision that affects lifecycle cost, machine uptime, and safety. That’s why our team offers detailed application consultations to ensure the right configuration is matched to your needs from the start.
Whether you’re upgrading heavy-duty driveshaft systems or sourcing components for new industrial machinery, taking the time to understand the difference between snap ring configurations can save significant costs down the line. If you’re looking for a reliable universal joint with inside snap ring, precision-manufactured to international standards and backed by consistent supply capabilities, we’d be glad to support your sourcing strategy with both product and expertise.
Contact Us