Material innovation plays a crucial role in the design and functionality of universal joints, particularly those with pressed bearings. By using specialized materials, manufacturers can produce universal joints that are not only lighter but also more durable and efficient. One of the standout features of universal joints with pressed bearings is the ability to reduce weight without sacrificing strength, making them ideal for high-performance applications. This unique combination of lightweight construction and superior performance has made them a popular choice for industries such as automotive, aerospace, and heavy machinery. In this article, we will delve into how material advancements are reshaping universal joints and why these innovations are essential for businesses seeking optimal performance.
At the core of these innovations is the choice of materials used in the pressed bearings themselves. Traditional bearings often rely on bulkier components, which can add unnecessary weight and reduce efficiency. Universal joints with pressed bearings, however, use advanced alloys and composite materials, which allow for thinner cup bodies while maintaining, or even improving, overall strength and performance. This means that vehicles or machinery can experience smoother operation and reduced fuel consumption, thanks to the lighter components. Such performance improvements directly contribute to cost savings, a major consideration for businesses looking to optimize their equipment’s operation.
Another key benefit of the materials used in universal joints with pressed bearings is their resistance to wear and corrosion. Premium materials, such as high-strength steel or even specialized coatings, offer better resistance to harsh environmental conditions, including high temperatures and exposure to moisture or chemicals. This enhanced durability ensures a longer lifespan for the universal joints and reduces the frequency of maintenance or replacements, which is vital for businesses that rely on continuous operation. Moreover, the ability to withstand high torque and pressure without compromising integrity is crucial for vehicles and machinery operating under heavy loads.
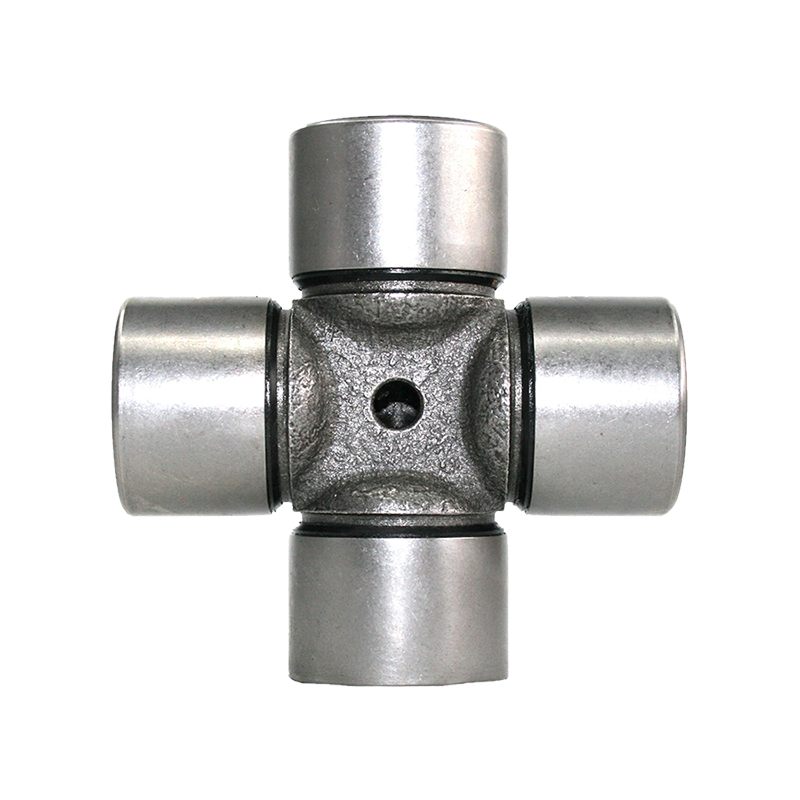
The shift toward specialized materials has not only improved the physical performance of universal joints but also addressed some of the environmental concerns associated with traditional materials. Lighter components help reduce the overall weight of the drivetrain, which, in turn, contributes to better fuel efficiency and lower emissions. As industries continue to prioritize sustainability, the demand for universal joints with pressed bearings made from advanced, eco-friendly materials is expected to grow. These materials allow businesses to meet stricter environmental regulations without sacrificing the performance they rely on.
In addition to these technical benefits, the incorporation of cutting-edge materials in universal joints opens up new possibilities for design flexibility. Manufacturers now have the freedom to explore more compact, efficient, and customized solutions that fit the specific needs of different industries. For instance, lightweight universal joints are increasingly sought after in the automotive sector for their ability to enhance vehicle dynamics without compromising structural integrity. The result is a perfect balance between performance and design that caters to the evolving demands of high-performance vehicles and equipment.
While the adoption of these advanced materials is already proving to be a game-changer, it is important to note that not all universal joints are created equal. There are significant differences between standard models and those using pressed bearings, particularly when it comes to performance under extreme conditions. For businesses in sectors like motorsports or industrial machinery, where every ounce of weight savings and performance gain matters, investing in universal joints with pressed bearings can make a tangible difference in operational efficiency. These joints are designed to handle higher speeds, heavier loads, and more aggressive operating conditions without the typical wear and tear seen in conventional joints.
In conclusion, the material innovations behind universal joints with pressed bearings are transforming the way businesses approach power transmission and efficiency. By leveraging advanced materials that reduce weight while boosting strength, durability, and performance, manufacturers can offer products that meet the rigorous demands of today’s industries. Whether you’re in automotive manufacturing, aerospace, or heavy machinery, investing in high-quality universal joints with pressed bearings is a strategic choice that will deliver long-term benefits. As technology continues to advance, we can expect even greater innovations in universal joint materials, further enhancing their role in high-performance applications.
Contact Us