This robust component is designed not just to transmit rotational motion but to thrive under extreme conditions where traditional joints might falter. From environmental adaptability to handling dynamic loads, these specialized universal joints are engineered to meet the demands of rugged terrains and punishing workloads. Let’s dive into the challenges they face and how they rise to the occasion.
One of the most pressing concerns for any heavy-duty vehicle component is its ability to withstand harsh environments. Whether it's scorching heat, freezing cold, or relentless exposure to moisture and dust, the universal joint with slotted bearings must perform without compromise. The design incorporates features that mitigate the effects of such conditions. For instance, corrosion-resistant coatings and advanced lubrication systems ensure that the bearing cups maintain their integrity over time. These enhancements make the slotted bearing universal joint particularly well-suited for industries like mining and construction, where vehicles often operate in abrasive and corrosive settings. By addressing environmental factors head-on, this design ensures longevity and reliability, even when the going gets tough.
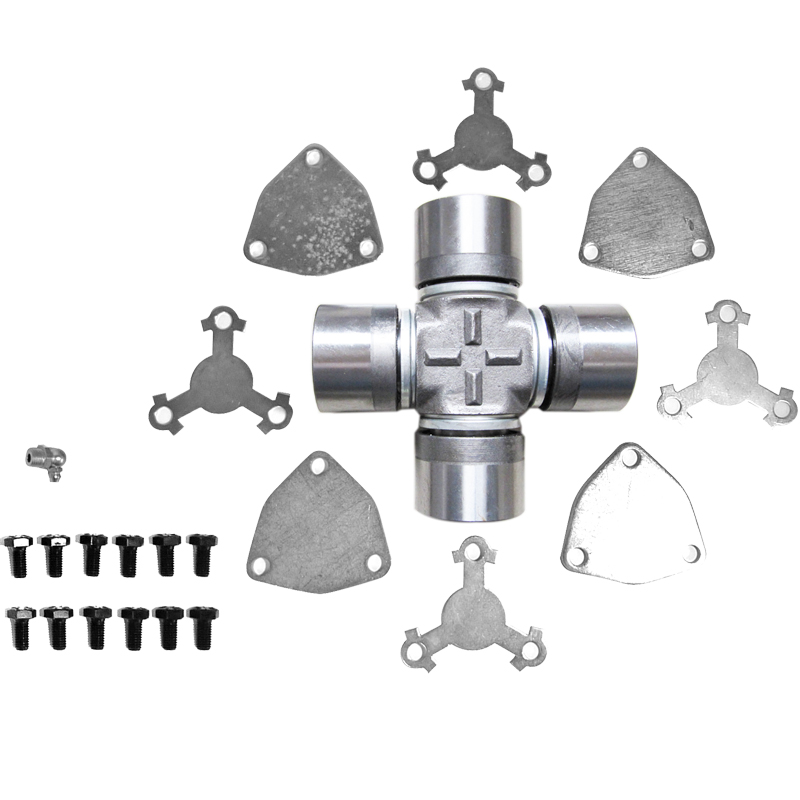
But environmental resilience is only part of the equation. Another critical aspect is how these joints handle dynamic loads, especially in off-road scenarios. Picture a Japanese truck navigating uneven terrain, where every bump and jolt places immense stress on the drivetrain. Here, the slotted groove and bolted mounting system shine. Unlike traditional press-fit designs, the slotted bearing configuration minimizes backlash and misalignment issues, ensuring smooth power transmission even under unpredictable conditions. The geometry of the slotted groove plays a pivotal role, distributing load forces evenly across the joint. This reduces wear and tear while maintaining consistent performance, which is crucial for operators who rely on their vehicles day in and day out.
Of course, no discussion about universal joints would be complete without touching on vibration management. Excessive vibration can lead to premature failure, increased maintenance costs, and reduced operational efficiency. The bolted mounting system of the slotted bearing universal joint helps dampen vibrations, providing a more stable connection between the driveshaft and other components. This feature is particularly beneficial in high-torque applications, where precision and stability are paramount. By reducing vibration-related stress, the joint not only extends its own lifespan but also protects surrounding parts from unnecessary strain.
Moreover, the integration of modern materials further enhances the capabilities of this design. Engineers often select hardened alloys and specialized steels that offer superior fatigue resistance and durability. These materials are chosen based on their ability to endure cyclic loading without succumbing to cracks or deformation. Combined with precision machining techniques, this material selection ensures that the slotted bearing universal joint remains a reliable choice for heavy-duty operations. It’s this blend of thoughtful engineering and cutting-edge materials that sets it apart from conventional alternatives.
The universal joint with slotted bearings isn’t just another component—it’s a testament to innovation in heavy-duty vehicle design. Its ability to adapt to environmental extremes, manage dynamic loads, and reduce vibration makes it indispensable for industries that demand peak performance. Whether you’re operating in the harshest climates or tackling the toughest terrains, this type of joint proves time and again why it’s trusted by professionals worldwide. So next time you’re evaluating drivetrain solutions, consider the unmatched versatility and resilience of slotted bearing universal joints—they’re built to go the distance.
Contact Us