When it comes to power transmission in heavy-duty applications, the question of torque capacity is always at the forefront of engineering discussions. Specifically, how much torque can a universal joint with wing bearings handle under continuous operation versus intermittent shock loads? This isn’t just a technical detail—it’s a critical factor that determines the reliability and longevity of your machinery. Whether you’re designing industrial equipment, agricultural vehicles, or off-road systems, understanding the performance limits of these components will help you make smarter decisions.
Universal joints equipped with wing bearings are renowned for their ability to transfer high levels of torque while accommodating angular misalignment. But what sets them apart is their unique design, which relies on mechanical keys and slots rather than traditional needle bearings. This feature not only enhances durability but also allows these joints to excel in environments characterized by fluctuating loads or sudden shocks. Under continuous operation, the maximum torque capacity of a wing-bearing u-joint largely depends on factors such as material composition, heat treatment, and the precision of machining. For instance, high-strength steel alloys and advanced surface treatments can significantly boost the load-bearing capabilities of the joint, enabling it to sustain steady torque levels over extended periods without compromising performance.
On the other hand, when subjected to intermittent shock loads—such as those encountered in mining equipment or construction machinery—the dynamics change. Shock loads introduce sudden spikes in torque that can stress even the most robust driveline components. Here, the wing bearing design truly shines. The mechanical allowance provided by the keys and slots ensures that the torque is distributed evenly across the bearing blocks, minimizing the risk of failure. However, it’s important to note that the maximum torque capacity during shock events is typically lower than under continuous operation. This is because shock loads generate instantaneous forces that exceed the steady-state limits of the material. To mitigate this, engineers often specify safety margins or opt for reinforced versions of the u-joint to ensure they can withstand these extreme conditions.
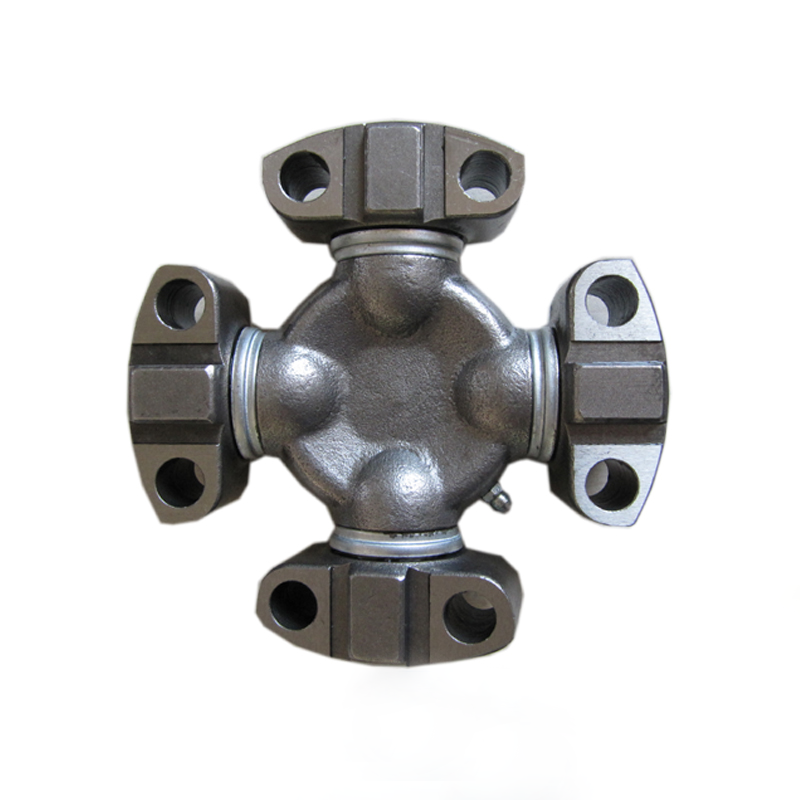
Another aspect worth considering is the role of lubrication in maintaining optimal torque capacity. While universal joints with wing bearings are designed for durability, proper lubrication remains essential to reduce friction and wear, especially under high-torque scenarios. Some models come with sealed or self-lubricating options, which are ideal for hard-to-reach installations or environments where regular maintenance isn’t feasible. By reducing the need for frequent servicing, these features not only enhance operational efficiency but also extend the lifespan of the joint.
From an application perspective, the versatility of wing-bearing universal joints makes them indispensable across various industries. In agriculture, for example, tractors and plows rely on these components to handle the constant torque demands of tilling soil, as well as the occasional jolts from uneven terrain. Similarly, in the automotive sector, off-road vehicles benefit from the shock-absorbing properties of wing-bearing u-joints, ensuring smooth power delivery even in rugged conditions. Industrial machinery, too, leverages their robustness to maintain productivity in assembly lines and conveyor systems.
So, how do you determine the right torque capacity for your specific needs? Start by evaluating the operating conditions of your application. Are you dealing with consistent loads, or will the system experience frequent shocks? Once you’ve identified the primary stressors, consult the manufacturer’s specifications to find a model that matches your requirements. Many suppliers provide detailed charts and graphs illustrating the relationship between torque, speed, and angular misalignment, helping you make an informed choice. Additionally, don’t hesitate to reach out to technical support teams—they can offer valuable insights into customizing the joint to meet your exact specifications.
In conclusion, whether you’re focused on continuous operation or preparing for intermittent shock loads, universal joints with wing bearings offer a reliable solution for demanding applications. Their ability to balance high torque capacity with exceptional durability makes them a standout choice for engineers and designers alike. By understanding the nuances of their performance under different conditions, you can maximize the efficiency and resilience of your driveline systems. After all, when it comes to torque transmission, having the right tool for the job isn’t just about meeting expectations—it’s about exceeding them.
Contact Us