When selecting a universal joint (U-joint) for heavy-duty applications, one of the most critical factors to consider is the torque capacity of the U-joint. This directly impacts the performance and longevity of the driveline system, especially in industries like automotive, construction, and agriculture, where U-joints are subjected to high stresses. Ensuring that the torque levels match the U-joint model is essential to prevent premature failure, minimize maintenance costs, and maintain the reliability of the machinery or vehicle.
U-joints are designed to transmit rotary motion and torque between two shafts that are not aligned, typically in drivetrains of vehicles or heavy machinery. Heavy-duty U-joints, in particular, are engineered to handle much higher levels of stress compared to standard models. The torque rating of a U-joint determines its ability to withstand the rotational forces applied during operation. If the torque requirements of the system exceed the U-joint's capacity, it can lead to deformation, bearing failure, or even catastrophic breakage. The key is to ensure that the U-joint you choose can comfortably handle the expected torque load in the application. For instance, trucks that rely on heavy-duty U-joints, like those in the 5-280X or 5-279X series, require U-joints that can handle significant amounts of torque, as these vehicles are tasked with moving heavy loads over long distances.
When determining the appropriate torque level for a U-joint, it’s essential to first understand the specific requirements of the application. This includes the type of vehicle or machinery, the weight it is carrying, and the types of forces that will be acting on the U-joint. The torque required will vary significantly between a heavy-duty truck and a smaller agricultural vehicle, so it is important to match the U-joint’s torque rating with the system’s demands. For example, in a truck drivetrain, the U-joint needs to withstand high axial loads and high-speed rotation, often under variable conditions, such as during acceleration or deceleration. Heavy-duty U-joints used in these contexts are typically rated for higher torque values and are built with materials such as alloy steel, which offers superior strength and durability.
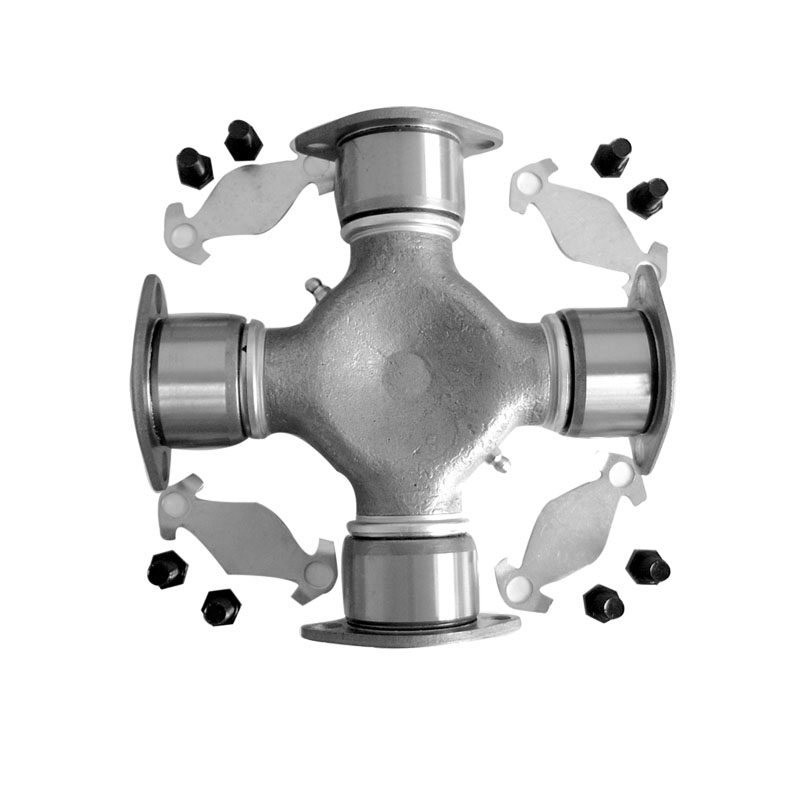
Another critical consideration when matching torque levels with U-joint models is the design of the U-joint itself. U-joints come in various types, including outside lock, flanged, and welded models, each with different torque capacities. Outside lock U-joints, which are commonly used in large U.S. trucks, for example, offer robust performance and are designed to handle higher torque levels. These U-joints are equipped with welding plate bearings that offer additional support and stability, ensuring the joint can manage high rotational forces without failure. For heavy-duty vehicles like the 5-280X series, choosing a U-joint with a higher torque capacity ensures that the drivetrain can handle the substantial loads required for long-haul trucking. In contrast, for lighter-duty applications, such as small agricultural equipment, a U-joint with a lower torque rating may suffice.
It's also important to note that U-joint failures often occur when the torque exceeds the design limits of the joint. Over-torquing can lead to the shearing of pins, bending of the U-joint yokes, or the breakdown of the bearings. The result is not only downtime for repairs but potentially costly damage to other drivetrain components. To prevent this, it’s essential to regularly assess the torque loads and match them accurately to the U-joint's capabilities. Additionally, U-joint maintenance is crucial—periodic lubrication, inspection for wear, and monitoring for signs of stress (such as unusual vibrations or noises) can help detect early signs of failure before they lead to significant damage. Regular maintenance helps ensure the U-joint continues to perform within its rated torque limits, extending its lifespan and maintaining the efficiency of the entire system.
When choosing a U-joint for heavy-duty applications, the torque capacity is a critical factor that should not be overlooked. Understanding the torque requirements of the system, selecting the right U-joint model that can handle those forces, and ensuring proper maintenance practices are in place are all essential steps to ensure optimal performance and prevent failure. By carefully matching torque levels with the right U-joint, operators can minimize downtime, reduce repair costs, and improve the overall longevity and reliability of the vehicle or machinery.
Contact Us