The universal joint with slotted bearings has emerged as a game-changer in the world of heavy-duty driveline components, especially for Japanese trucks that demand durability, stability, and ease of maintenance. One of the defining features of this universal joint design is the slotted groove at the base of each bearing cup. This unique structure accommodates a retention plate, which secures the cups in place with bolts. While the innovation may appear straightforward, it has revolutionized how these joints are installed and replaced, making maintenance not only faster but also far more reliable.
When it comes to the initial installation, the slotted bearing design offers substantial advantages over conventional universal joints. Typically, fitting bearing cups into place in a standard joint requires precise alignment and securing, a process that can be tedious and time-consuming. With slotted bearings, however, the grooves provide an intuitive alignment guide. The cups are firmly held by the slots, ensuring they are perfectly positioned before bolting. This approach simplifies the technician’s task, reducing the need for adjustments or realignments. As a result, the installation process is faster, and the risk of misalignment, which can cause premature wear or even component failure, is minimized. This slotted design is especially appreciated in heavy-duty vehicles, where servicing large and powerful driveline components can otherwise be labor-intensive and challenging.
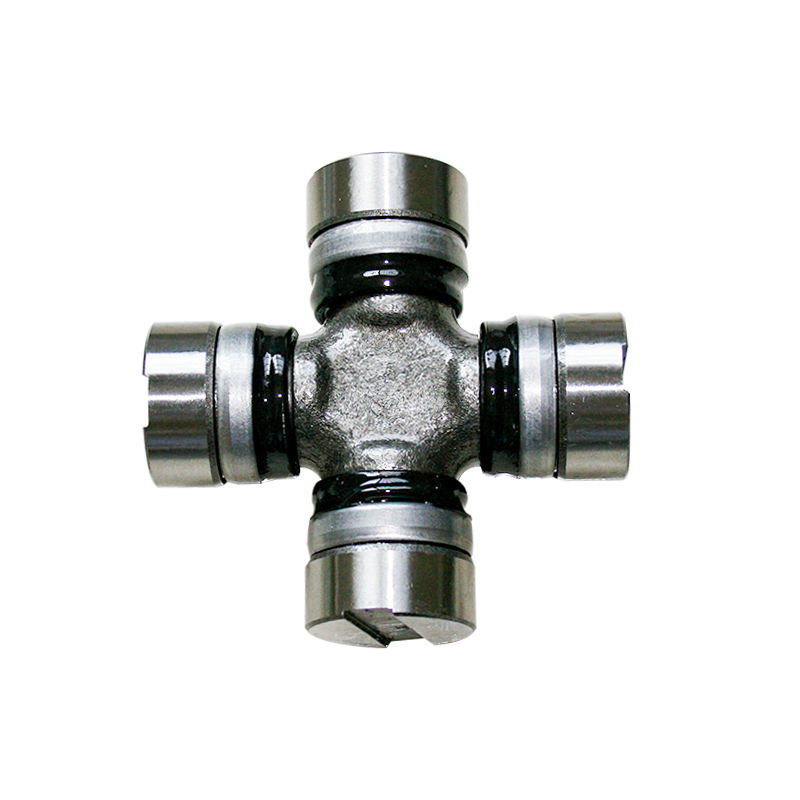
The ease of replacement also benefits greatly from the slotted bearing structure, particularly for vehicles subjected to heavy loads and rough terrains, as these joints tend to experience significant wear. Over time, bearing cups can sometimes shift due to vibration and constant strain, a common issue in high-demand applications. However, with slotted bearings, the risk of these cups slipping or loosening is reduced since the retention plate locks the cups securely in place. When it’s time to replace the joint, technicians find it simpler to remove the bolts and slide out the joint, as the groove design effectively “guides” the cups out without resistance. The reduction in disassembly time is notable, making it an ideal design for large fleets where vehicles need to be back in service quickly to avoid downtime costs.
Another factor that enhances both installation and replacement is the secure, vibration-resistant structure of the slotted bearing joint. Unlike standard bearings that rely on a press fit or similar methods, slotted bearings remain reliably secured by the retention plate. This feature minimizes the risk of the joint loosening over time, reducing the need for frequent inspections or re-tightening, common with conventional joints in heavy-duty vehicles. This reliability is essential for trucks that operate in challenging environments, where exposure to dirt, moisture, and temperature extremes can weaken other types of fittings. The bolt-secured slotted bearing joints hold steady, providing a long-lasting fit that withstands constant movement and stress, thereby extending the service intervals between replacements.
Cost considerations also favor the universal joint with slotted bearings design. Although these universal joints may have a slightly higher initial price, the time savings on installation, reduced replacement frequency, and minimized maintenance labor significantly offset upfront costs. For heavy-duty truck operators and fleet managers, this translates into reduced vehicle downtime and fewer disruptions to operations. Additionally, this design supports compatibility across various vehicle models, which is particularly beneficial for fleets that use a mix of heavy-duty Japanese trucks. Technicians can quickly adapt to the uniform installation and replacement processes, regardless of the specific truck model, creating further efficiencies and reducing the learning curve associated with component maintenance.
Contact Us