Maintenance-free universal joints have transformed machinery reliability by eliminating the need for routine lubrication, but their secret lies in cutting-edge seal technology. These joints, engineered to thrive in harsh conditions, rely on innovative sealing mechanisms to lock out contaminants and retain lubricants for life. For engineers and operators, understanding how these seals balance protection and performance is key to maximizing uptime and efficiency.
Seal Design: The First Line of Defense
At the heart of every maintenance-free universal joint is a meticulously engineered sealing system. Unlike traditional greaseable joints, which depend on periodic lubrication to counteract wear, maintenance-free variants use advanced seals—often made from nitrile, fluorocarbon, or polyurethane—to create airtight barriers. These materials are chosen for their resistance to temperature extremes, chemicals, and abrasion. For instance, labyrinth seals, which feature interlocking grooves, act as a physical maze to block dust, water, and debris while allowing minimal friction. Meanwhile, elastomer seals adapt dynamically to temperature shifts, maintaining integrity in both arctic cold and desert heat.
But sealing technology isn’t just about exclusion—it’s also about retention. The lubricant inside a maintenance-free universal joint must stay viscous and evenly distributed over decades. Engineers achieve this by pairing seals with specialized lubricants, such as lithium-complex greases or synthetic oils infused with anti-wear additives. These formulations resist oxidation and shear degradation, ensuring consistent performance even under high-speed or high-load conditions.
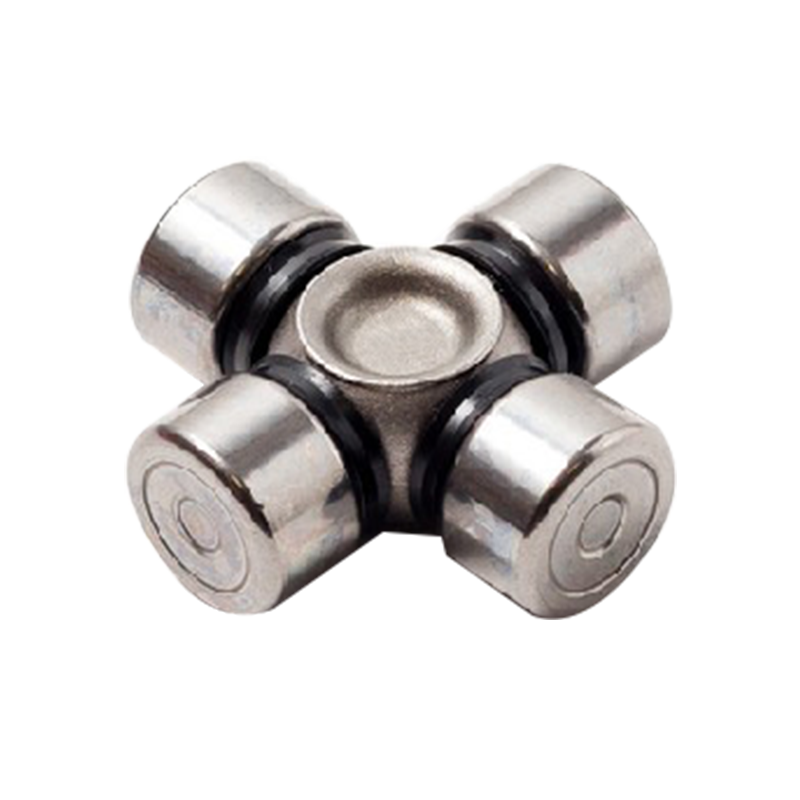
Balancing Durability and Efficiency: The Friction Trade-Off
While seals are critical for contamination prevention, they introduce a challenge: friction. Every seal adds slight rotational resistance, which can impact energy efficiency, especially in high-RPM applications. To mitigate this, manufacturers employ low-friction polymers and precision-engineered geometries. For example, lip seals—thin, flexible membranes that contact the joint’s bearings—minimize contact area while maintaining a tight seal. Similarly, non-contact seals use narrow gaps to separate components, reducing drag without compromising protection.
The interplay between seal durability and rotational efficiency also depends on application-specific demands. In agriculture, where machinery faces constant dust and shock loads, heavy-duty seals with reinforced edges prioritize longevity. Conversely, automotive drivetrains might prioritize low-friction designs to enhance fuel efficiency. Engineers must weigh these factors during selection, ensuring the maintenance-free universal joint aligns with the operational environment.
Real-World Impact: From Factories to Farms
The advancements in seal technology have made Maintenance-free universal joints indispensable across industries. In automotive manufacturing, robotic arms equipped with these joints operate 24/7 without lubrication breaks, slashing downtime. In agriculture, harvesters navigating dusty fields maintain peak performance season after season, thanks to seals that repel debris. Even marine applications benefit: saltwater-resistant seals prevent corrosion in propeller shafts, extending service life in harsh maritime conditions.
Conclusion: A Leap Forward in Engineering
Maintenance-free universal joints represent more than convenience—they’re a leap in reliability engineering. By integrating advanced seal technology with lifelong lubrication, they eliminate a historic pain point for industries reliant on heavy machinery. As seal materials and designs continue to evolve, these joints will only grow more versatile, cementing their role as unsung heroes of modern mechanics. For businesses prioritizing uptime and cost savings, adopting this innovation isn’t just smart—it’s essential.
Contact Us