The universal joint with wing bearings represents a paradigm shift in torque transmission technology, particularly for applications demanding robustness under dynamic loads. Unlike traditional needle-bearing U-joints, this design leverages a mechanical allowance system where keys and slots replace rolling elements, offering enhanced durability and adaptability. To fully harness its potential, engineers must focus on three core structural and mechanical optimization strategies: geometric precision of keyways, tolerance compatibility between mating components, and dynamic stability under asymmetric loads.
Keyway Geometry: Balancing Stress Distribution and Torque Efficiency
The geometric design of keyways in wing-bearing universal joints directly influences stress concentration and torque transmission efficiency. Finite element analysis (FEA) studies reveal that trapezoidal or involute-shaped keyways outperform rectangular profiles by reducing localized stress peaks by up to 30% under shock loads. For instance, an involute design distributes shear forces more evenly across the contact surfaces, minimizing wear in high-cycle applications such as mining equipment drivetrains. Additionally, the angle of engagement between keys and slots must align with the joint’s maximum operating angle (typically 15°–25°) to prevent edge loading. Advanced manufacturing techniques like CNC broaching ensure micron-level accuracy in slot dimensions, critical for maintaining mechanical allowance without compromising backlash control.
Tolerance Engineering: Precision in Torque Transfer and Wear Mitigation
The interplay between tolerance specifications and long-term performance is a cornerstone of universal joint with wing bearings design. A slight interference fit between keys and slots can enhance torque transfer efficiency by eliminating micro-slip, but excessive tightness risks galling under thermal expansion. Conversely, a controlled clearance (0.02–0.05 mm) accommodates misalignment while reducing fretting corrosion—a common failure mode in oscillating applications like wind turbine pitch systems. Real-world testing shows that optimized tolerance pairing extends service intervals by 40% compared to traditional needle-bearing joints, particularly in environments with frequent load reversals. Furthermore, surface treatments such as nitriding or DLC (diamond-like carbon) coatings on keyways further mitigate wear, ensuring consistent performance over 50,000+ operating cycles.
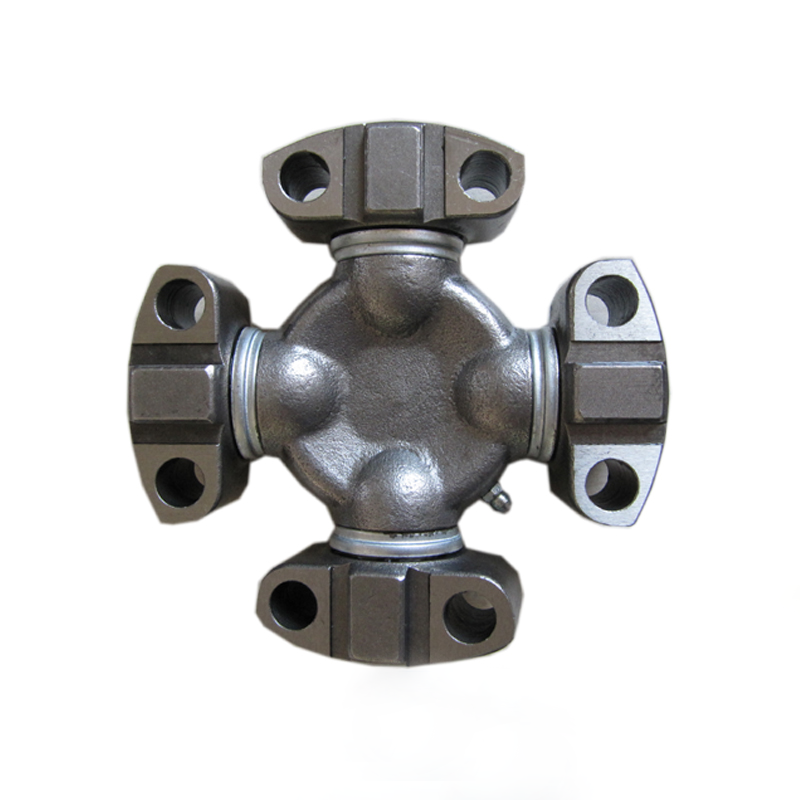
Dynamic Stability: Asymmetric Load Handling and Fatigue Resistance
In scenarios involving non-uniform loads—common in aerospace actuators or heavy-duty construction machinery—the wing-bearing universal joint’s structural symmetry becomes a critical factor. Asymmetric wing-bearing layouts, where bearings are offset to counteract torsional deflection, have demonstrated a 20% improvement in dynamic stability during rapid directional shifts. Computational fluid dynamics (CFD)-assisted lubrication analysis further reveals that strategically placed grease reservoirs within the bearing blocks reduce friction-induced heat generation by 15%, even at angular velocities exceeding 3,000 RPM. Rigorous fatigue testing under ISO 1143 standards confirms that optimized designs achieve a safety factor of 2.5 against keyway fracture, outperforming conventional U-joints in shock load resilience.
By prioritizing geometric precision, tolerance synergy, and dynamic load adaptability, the universal joint with wing bearings emerges as a durable, high-efficiency solution for industries ranging from automotive to renewable energy. Its mechanical allowance architecture not only addresses the limitations of traditional designs but also sets new benchmarks for reliability in extreme operating conditions. Engineers seeking to maximize uptime and minimize maintenance costs will find these structural innovations indispensable in next-generation drivetrain systems.
Contact Us