Universal Joint With Inside Snap Ring (U-joints) play a pivotal role in the mechanical world, connecting shafts with axes that are not perfectly aligned. Particularly, universal joints featuring an inside snap ring are designed to provide enhanced stability and reliability, making them a popular choice across various applications, from automotive drive shafts to industrial machinery. However, the efficiency and lifespan of these components can be significantly affected by angular misalignments, which occur when the shafts are not properly aligned during operation. Understanding how these misalignments influence performance is crucial for ensuring the longevity of the joint and the overall system in which it operates.
When angular misalignments occur, the universal joint is compelled to work harder to transmit torque and motion between the shafts. This additional strain can lead to increased wear on the internal components of the joint, including the cups and cross shaft. Over time, this accelerated wear can diminish the efficiency of power transmission, leading to energy losses that can affect the entire system's performance. Furthermore, the friction generated by misaligned components can produce excess heat, further exacerbating wear and tear. For joints equipped with an inside snap ring, the additional forces exerted due to misalignment can stress the snap ring mechanism, potentially leading to failure. If the snap ring fails, the connection could loosen, leading to catastrophic failures and significant downtime for repairs.
Moreover, the degree of angular misalignment plays a critical role in determining how quickly a universal joint might wear out. Minor misalignments may be manageable without severely impacting performance, but as the angle increases, the inefficiencies can compound rapidly. This scenario is especially prevalent in applications with high torque or load demands, where the stresses on the joint are magnified. Regular monitoring and maintenance are vital in these scenarios, as proactive measures can help identify misalignments before they lead to severe damage. Technicians should perform routine inspections to check for signs of excessive wear, unusual vibrations, or noise—indicators that the joint may be experiencing undue stress due to misalignment.
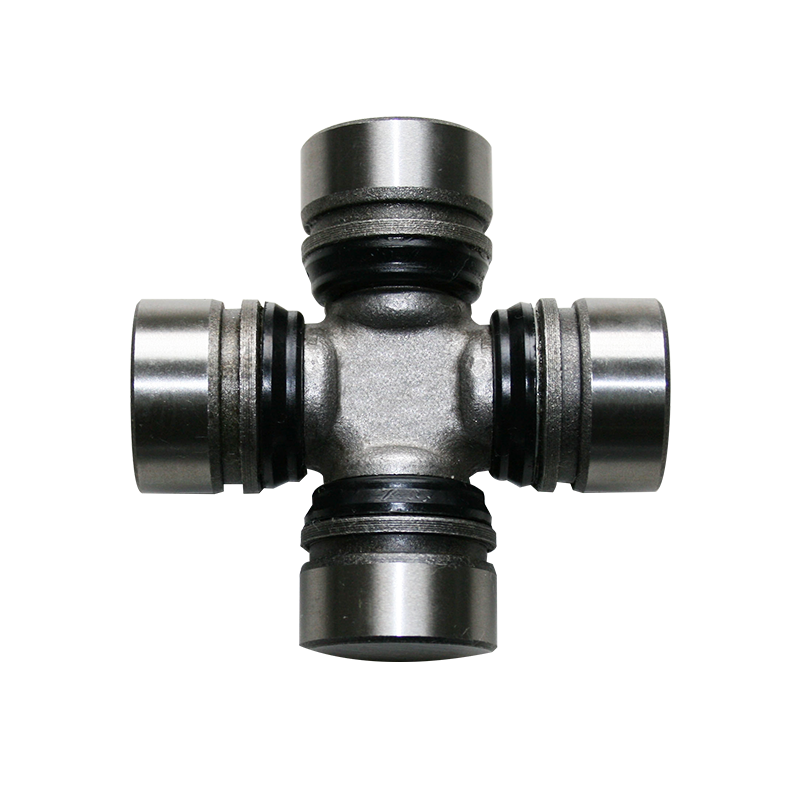
Another crucial aspect to consider is how environmental factors can exacerbate the effects of angular misalignments. For instance, operating in extreme temperatures or harsh conditions can further strain a universal joint, making it even more susceptible to misalignment-related issues. In such environments, the material properties of the cups and snap rings must be carefully chosen to withstand both the mechanical and thermal stresses. A well-chosen material can enhance the resilience of the joint, extending its lifespan despite the challenges posed by misalignments.
To mitigate the effects of angular misalignments, it is essential to adopt best practices during installation and maintenance. Ensuring proper alignment during the initial setup can dramatically reduce the risk of future issues. This can be achieved through precise measuring tools and alignment techniques that account for the specific application requirements. Additionally, employing lubricants designed to reduce friction and heat can further protect the internal components of the U-joint from the stresses induced by misalignment.
The impact of angular misalignments on the efficiency and lifespan of universal joints with inside snap rings cannot be underestimated. As these joints are subjected to misalignment, they face increased wear, potential failure of critical components like the snap ring, and reduced overall performance. By understanding the mechanics behind these relationships and implementing preventive measures, engineers and technicians can ensure that their systems operate smoothly and efficiently, extending the life of these essential components.
Contact Us