Universal joints with wing bearings, often referred to as mechanical U-joints, represent a unique and robust solution for torque transfer in various applications. These joints are characterized by their innovative design, which utilizes keys mated to corresponding slots in the connecting yokes. This key-and-slot configuration not only secures the joint but also enhances its ability to handle continuous load variations and shock loads—key factors that set them apart from traditional joint types.
When it comes to shock loading conditions, wing bearing designs excel due to their inherent structural advantages. The ability to absorb sudden forces is critical in environments where equipment is subjected to abrupt changes in torque, such as in automotive driveshafts or industrial machinery. Traditional universal joints, while effective in many situations, often lack the same level of shock absorption. Their design can lead to increased wear and potential failure when faced with intense or fluctuating loads. In contrast, the mechanical allowance provided by wing bearings allows for greater flexibility, reducing stress on the joint and surrounding components. This adaptability is crucial in applications characterized by dynamic conditions, where the ability to accommodate misalignments and shifts in load direction is paramount.
Another advantage of wing bearing universal joints is their durability under such stressful conditions. The keys that secure the Universal joints with wing bearings not only facilitate torque transmission but also distribute the stresses more evenly across the joint. This distribution minimizes localized stress points, which can lead to fatigue and eventual failure in less robust designs. As a result, wing bearing U-joints can provide a longer service life, even in high-shock environments. They are less prone to catastrophic failures, which can be detrimental in applications where safety and reliability are non-negotiable.
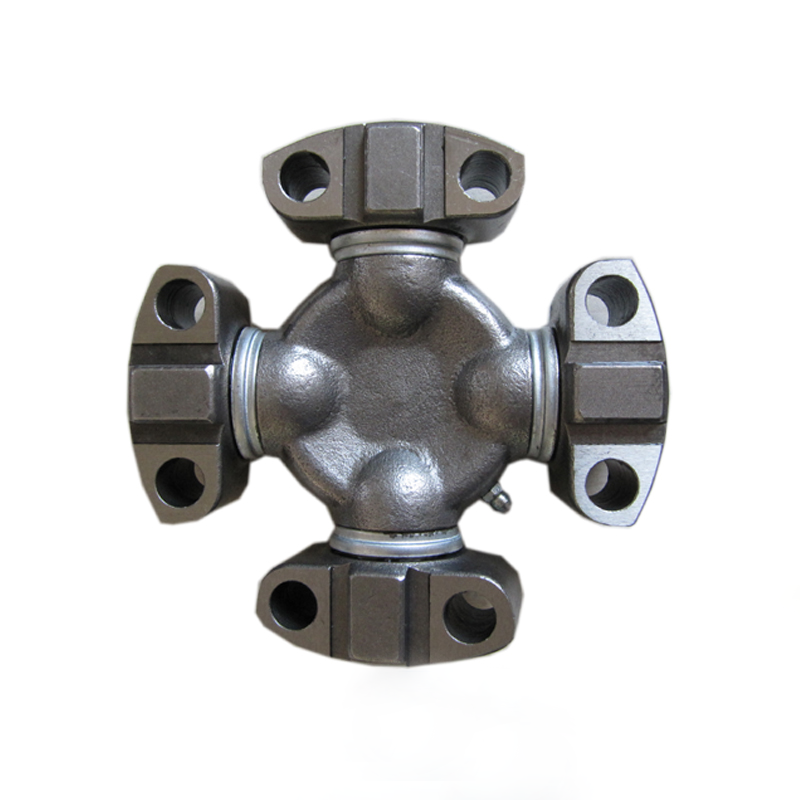
Moreover, the material choices often employed in the construction of these joints further enhance their performance under shock loads. High-strength alloys and advanced composites used in wing bearing designs contribute to their resilience and resistance to deformation. When comparing them to traditional U-joints, which may rely on standard steel components, it becomes clear that wing bearing joints offer a performance advantage in demanding situations. Their ability to withstand not just the shock loads but also the cyclical loading that often accompanies such conditions positions them as a superior choice in many applications.
In practical terms, those responsible for selecting and implementing universal joints should consider the specific requirements of their systems. While traditional joints may suffice in stable environments, the increased performance and reliability of wing bearing universal joints under shock loading conditions make them an attractive option for industries such as automotive, aerospace, and heavy machinery. The longevity and reduced maintenance needs associated with these designs can lead to lower overall operational costs, providing a compelling case for their adoption.
When it comes to managing shock loads, wing bearing universal joints shine due to their unique design and material properties. Their ability to absorb forces, distribute stress, and maintain functionality under challenging conditions makes them a preferred choice for applications that demand both resilience and reliability. As industries continue to evolve and face new challenges, the performance advantages of wing bearing designs will undoubtedly play a critical role in driving innovation and enhancing the durability of mechanical systems.
Contact Us