Cardan joints, also known as universal joints, are crucial components in various mechanical systems, providing flexibility and torque transmission between intersecting shafts. The materials used in manufacturing Cardan joints play a significant role in determining their performance, durability, and resistance to wear. Here are some commonly employed materials in the production of Cardan joints:
Steel Alloys:
Carbon Steel: Commonly used for the manufacturing of
Cardan joints due to its strength and durability.
Alloy Steels: Including elements like chromium and nickel to enhance corrosion resistance and strength.
Stainless Steel:
Offers excellent corrosion resistance, making it suitable for applications where exposure to moisture or harsh environments is a concern.
Bronze:
Used for bearing components within the joint due to its self-lubricating properties and wear resistance.
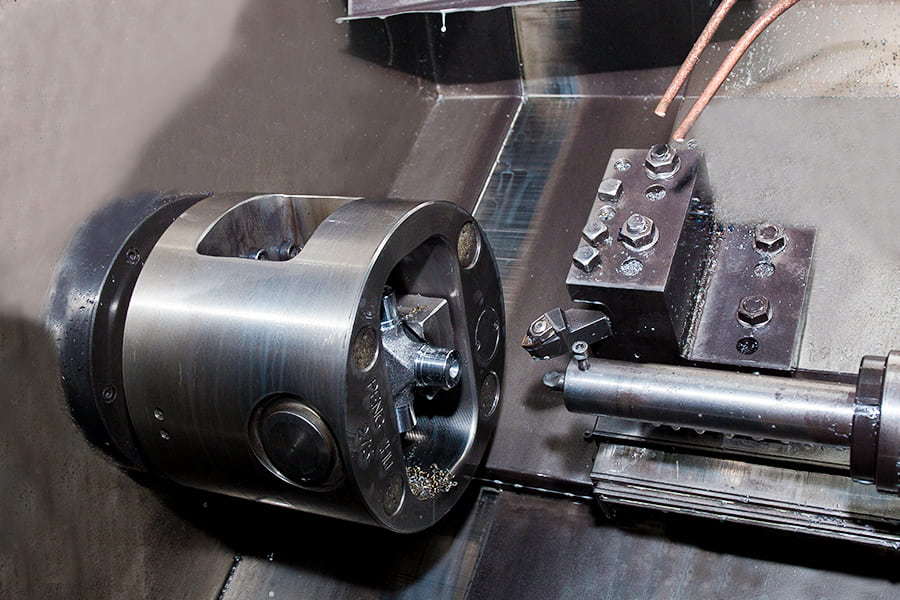
Aluminum:
Lightweight and corrosion-resistant, aluminum may be used in certain applications where weight reduction is a critical factor.
Cast Iron:
Provides high strength and wear resistance, suitable for heavy-duty applications.
Plastic and Polymer Composites:
In some cases, thermoplastics or reinforced polymer composites are used for non-load-bearing components to reduce weight and enhance corrosion resistance.
Heat Treatment:
Components, especially those subject to high loads, may undergo heat treatment processes such as carburizing or nitriding to improve hardness and wear resistance.
Contact Us