Heavy-duty universal joints (U-joints) are crucial components in heavy-duty machinery and vehicles, particularly in applications that demand exceptional strength and durability. Their primary role is to transfer torque and rotational motion between shafts that are not perfectly aligned, allowing for smooth operation even in challenging conditions. Unlike lighter-duty versions, heavy-duty universal joints are engineered to handle significantly higher levels of torque and vibration, which makes them essential in environments such as trucking, construction, and industrial machinery.
The ability of a heavy-duty universal joint to manage higher torque loads is largely attributed to its robust construction and materials. Typically made from high-strength steel alloys or other durable metals, these joints are designed to withstand the intense forces encountered in heavy-duty applications. The size and design of the components, such as the yokes and cross bearings, are scaled up compared to their lighter-duty counterparts, which helps distribute the stress more effectively and reduces the risk of failure. The precision engineering involved ensures that the joint maintains structural integrity even under extreme conditions, thereby providing reliable performance.
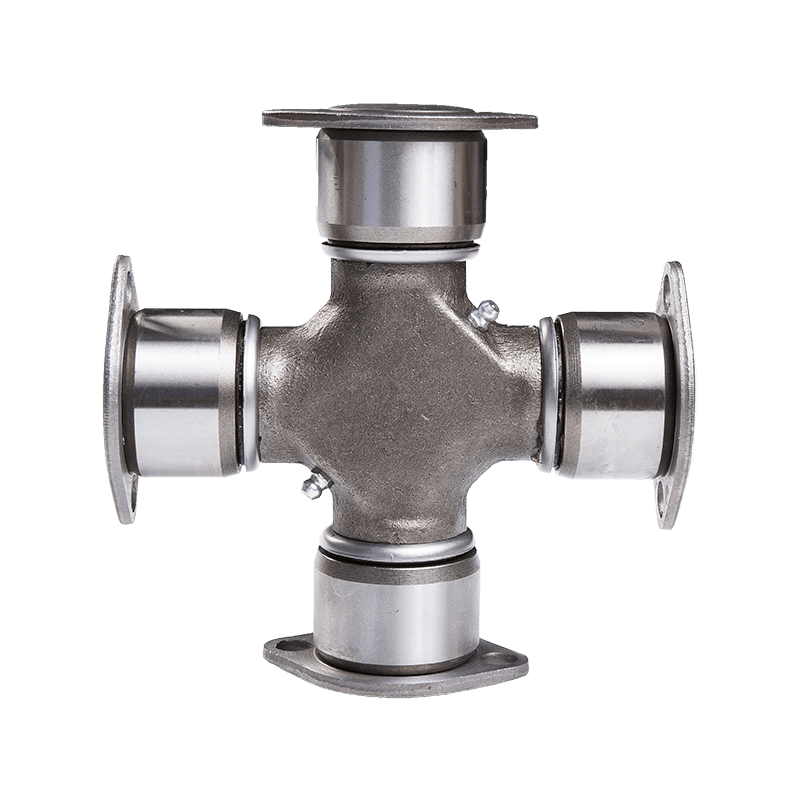
When it comes to vibration, heavy-duty universal joints are engineered with features that minimize the impact of oscillations and reduce noise. This is achieved through improved bearing designs and the use of advanced materials that absorb and dissipate vibrational forces more effectively. In contrast, lighter-duty universal joints may not have the same level of vibration dampening capabilities, leading to increased wear and tear over time. The enhanced vibration control in heavy-duty joints also contributes to a smoother and quieter operation, which is especially important in vehicles and machinery that operate at high speeds or under heavy loads.
Maintenance and longevity are also areas where Heavy-duty universal joints differ significantly from their lighter-duty counterparts. The increased robustness of heavy-duty joints means they typically require less frequent maintenance and can handle longer intervals between service checks. This durability translates to lower overall maintenance costs and less downtime, which is a critical factor for businesses relying on heavy-duty equipment. Regular inspection and proper maintenance are still essential, but the heavy-duty design inherently reduces the likelihood of premature failures or performance issues.
Heavy-duty universal joints handle torque and vibration differently from lighter-duty versions due to their superior construction and material choices. Their ability to manage higher torque loads and effectively dampen vibrations ensures they provide reliable and consistent performance in demanding applications. This durability not only enhances the operational efficiency of machinery and vehicles but also contributes to lower maintenance costs and increased longevity. As industries continue to push the limits of performance and reliability, the advancements in heavy-duty universal joint technology will remain a key factor in achieving optimal results in high-stress environments.
Contact Us